A Sustainable Solution for Safer, Cleaner E-Waste Metal Recovery
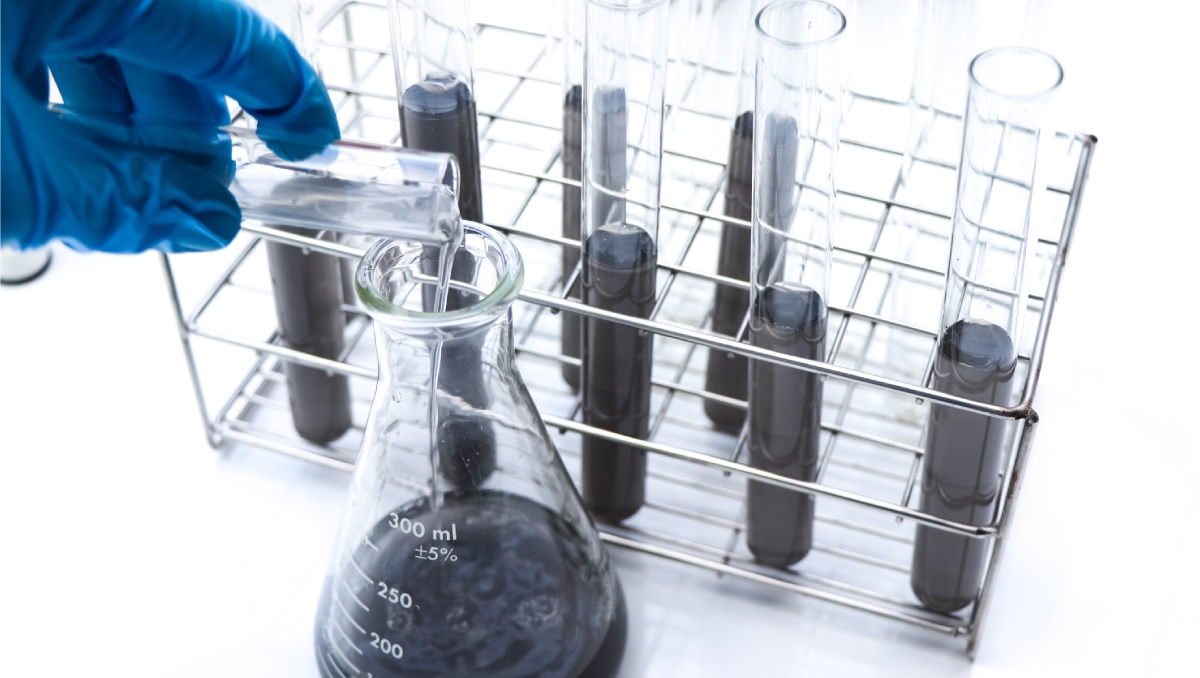
Date

An integrated multistage leaching process is projected for the selective extraction of metals from mobile printed circuit boards.Source: www.chemistry-europe.onlinelibrary.wiley.com
New Green Tech For E-Waste Metal Recovery
At D Block Metals, we understand that securing critical metals like lithium, cobalt, and nickel is essential to meeting the growing demand for energy storage and manufacturing technologies. However, traditional methods of recovering these metals from electronic waste (e-waste) often rely on harsh chemicals and energy-intensive processes that can harm the environment and increase costs. That’s why we’re excited about the innovative green technology emerging from the University of Kentucky, which is paving the way for a more sustainable future in metal recovery.
Hydrophobic Deep Eutectic Solvents (DESs)
Researchers at the University of Kentucky, with support from the U.S. Department of Energy, are developing plant-based solvents called hydrophobic deep eutectic solvents (DESs) to revolutionize the recovery of valuable metals from discarded electronics, spent batteries, and industrial waste. Unlike traditional recovery methods that rely on sulfuric acid or high temperatures, DESs offer a safer, more efficient, and environmentally friendly alternative.
Selective Metal Recovery for High Purity
One of the key advantages of this green tech is selective metal recovery. Tailoring the chemical properties of DESs allows for precise targeting of specific metals like lithium, cobalt, or nickel from complex e-waste. This selectivity reduces contamination and minimizes the need for additional purification steps, improving both recovery rates and overall process efficiency. For industries like electric vehicle battery manufacturing, where even trace impurities can impact performance, this precision is game-changing.
Cleaner Chemistry for Safer Workplaces
In addition to enhancing selectivity, DESs prioritize workplace safety and environmental responsibility. Traditional recovery processes expose workers to highly corrosive substances, increasing health risks and driving up costs due to equipment corrosion and hazardous waste disposal. In contrast, DESs are derived from renewable plant-based materials, making them biodegradable and less toxic. These solvents operate under mild conditions, reducing worker exposure to harmful chemicals while cutting down on the safety infrastructure required for traditional processes.
Reducing Waste Through Solvent Recycling
Waste reduction is another area where this green technology excels. Conventional recovery systems often rely on single-use solvents that are discarded after processing, contributing to high operational costs and environmental damage. The University of Kentucky research team is addressing this issue by developing membrane separation technologies that enable DESs to be recycled and reused repeatedly without losing effectiveness. This innovation not only reduces waste but also drives down costs, aligning perfectly with the principles of a circular economy.
A Path Toward a Sustainable Metal Recovery Future
At D Block Metals, we see this research as a significant step toward transforming metal recovery operations across industries. By adopting greener and more efficient processes, we can reduce our environmental footprint, improve worker safety, and lower production costs, all while securing a reliable supply of critical metals. This type of sustainable innovation is crucial as the demand for energy storage solutions and advanced manufacturing materials continues to grow.
As the e-waste problem expands globally, solutions like DESs can reshape how we think about recycling and resource recovery. At D Block Metals, we are committed to staying at the forefront of advancements like this to better serve our partners and contribute to a cleaner, more sustainable future. We believe that the future of metal recovery lies in technologies that value people, the planet, and long-term industrial growth.