What the new Cu-Ta-Li Alloy Means for Tantalum Recyclers
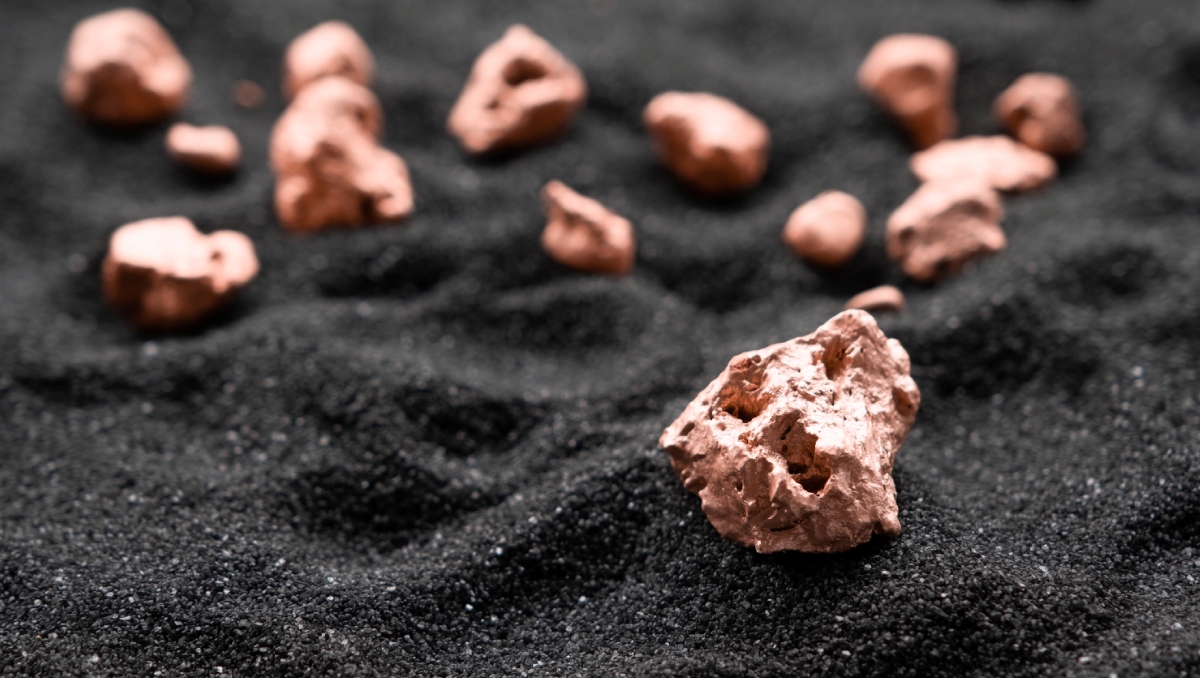
Date
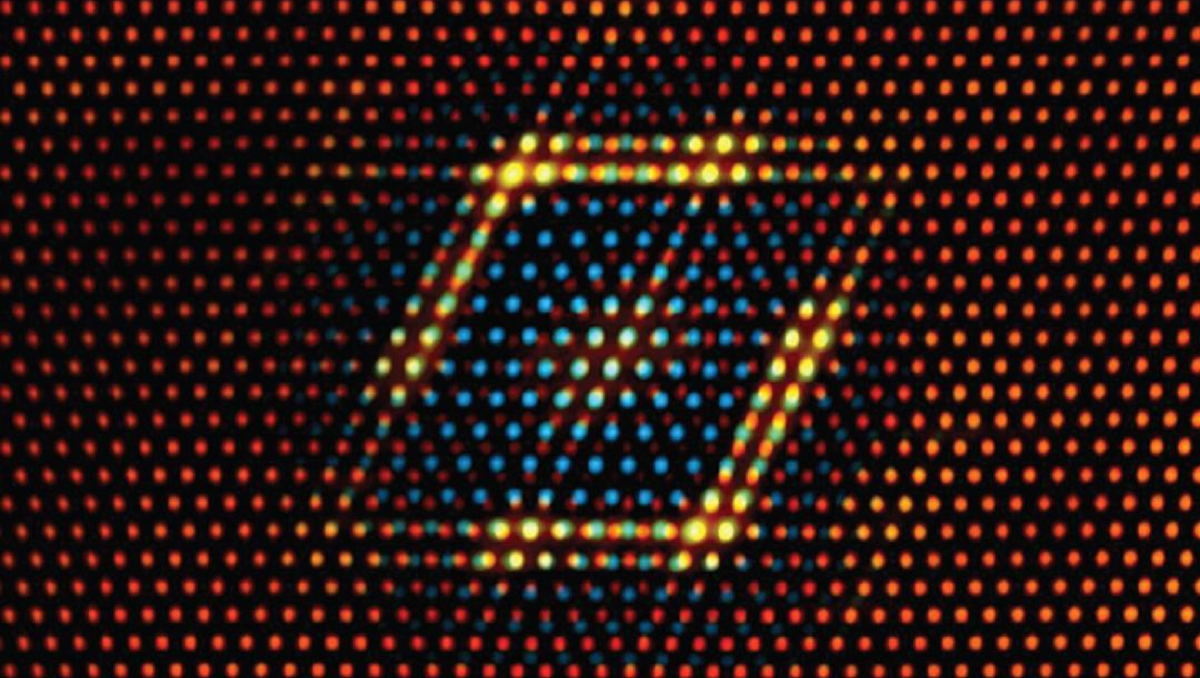
"This groundbreaking nanostructured copper alloy that could redefine high-temperature materials for aerospace, defense and industrial applications."Source: news.lehigh.edu
Lehigh University
Copper’s New Superalloy
At D Block Metals, we closely monitor the metals research shaping tomorrow’s materials and markets. One of the most exciting recent developments is the discovery of a nanostructured copper-tantalum-lithium (Cu-Ta-Li) alloy that exhibits superalloy-like strength at high temperatures while retaining copper’s hallmark conductivity. This material, developed by the U.S. Army Research Laboratory and Lehigh University, could soon impact aerospace, defense, and industrial sectors but it also carries strategic implications for tantalum recyclers.
What Makes This Alloy a Breakthrough?
The Cu-Ta-Li alloy represents a new class of high-performance materials. Through nano-structuring and an innovative complexion-stabilized precipitate design, the researchers have created a material that maintains mechanical strength and structural stability under extreme heat and stress conditions where traditional copper alloys would fail.
The secret lies in the formation of Cu₃Li precipitates stabilized by tantalum-rich atomic bilayer complexions. These complexions suppress grain growth, effectively “locking in” the nanoscale structure that gives the alloy its strength. Even after 10,000 hours at 800°C, the alloy resists degradation, making it one of the most heat-stable copper materials ever made.
Why This Matters for Tantalum Recyclers
For those of us in the tantalum recovery and recycling sector, the inclusion of tantalum as a key stabilizing element in a potentially mass-produced alloy has direct consequences:
Rising Demand for Tantalum in Structural Alloys
Historically, tantalum’s demand has been driven by its use in capacitors, surgical implants, and superalloys for aerospace turbines. If the Cu-Ta-Li alloy enters widespread use across military, aerospace, and industrial heat-transfer systems, tantalum will be needed not just in trace quantities but as an engineered component in base metals.
Pressure on Primary Supply Chains
Tantalum is classified as a critical mineral due to its limited sources and high strategic value. With new applications emerging, global supply could tighten further. For recyclers, this creates a prime opportunity in which secondary tantalum recovery will play a larger role in meeting industrial demand and stabilizing pricing.
Shift in Recycling Streams
As alloys like Cu-Ta-Li become integrated into military and industrial manufacturing, scrap streams will evolve. Recyclers will need to identify, separate, and process new forms of tantalum-bearing materials, not just electronic components but structural copper-based scrap that contains tantalum at nanoscale concentrations.
Technology-Driven Recovery Strategies
The nanostructured nature of the Cu-Ta-Li alloy presents unique challenges. Conventional recycling methods may not detect or separate tantalum embedded within copper matrices at the nanoscale. Advanced techniques such as electron microscopy, selective leaching, and spectroscopic analysis will be essential for maximizing tantalum recovery from these future materials.
Strategic Positioning for the Recycling Sector
At D Block Metals, we’re already exploring how discoveries like these will influence future material flows. As tantalum takes on a new metallurgical role, recyclers must prepare by:
- Tracking alloy adoption in defense and aerospace sectors.
- Investing in technology to identify and process complex multi-metal structures.
- Partnering with manufacturers to close the loop on post-industrial and post-consumer tantalum-bearing materials.
- Building inventory and refining processes to support increased demand and pricing volatility.
Looking Ahead
The U.S. Army Research Laboratory has secured a U.S. patent (US 11,975,385 B2) for the Cu-Ta-Li alloy, signaling long-term interest in its deployment. As military programs transition from prototyping to production (especially in hypersonic vehicles and thermal management systems) demand for tantalum will follow.
We see this development not as a challenge, but as an opportunity for innovation in recovery. By staying ahead of metallurgical trends and preparing for the next generation of advanced alloys, D Block Metals remains committed to ensuring that critical elements like tantalum stay in circulation, supporting both national security and sustainable resource use.